Efficacy and Application Areas
of «RIKOR» Series X-ray Diffractometer
|

|
Every purchase of an instrument should bring to customer a direct or indirect benefit.
The efficacy of using a «RIKOR» Series X-ray diffractometer is determined by its intended purpose. «RIKOR» provides for nondestructive direct check for stress condition in parts and structures. Such inspection enables detection and remedy of adverse factors during manufacture and operation of parts and facilities. The adverse factor consists in creation of large tensile residual stresses, which, when imposed with effective tensile stresses, can result in defects during manufacture or a fault, accident or catastrophe during operation of parts and facilities.
|

|
Application 1.
Analysis in Parts of a Satellite Made of Titanium Alloy
|

|
Object of check – a satellite part made of titanium alloy VT23.
Purpose of check – to assess stress condition in semi-spheres of satellite part at different state of their manufacture: before the flanges are welded in (operation 1), after the flanges are welded in (operation 2), and after thermal processing (operation 3).
Check was performed at the premises of S.P. Korolev ENERGIA RKK OJSC, the participants being A.V. Lyuttsau, Dr. Eng. Sc. A.V. Kotelkin, Dr. Phys. Math. Sc. A.D. Zvonkov, Dr. Eng. Sc. D. B. Matveev, Dr. Eng. Sc. V.N. Sereda, A.V. Gollandtsev.
|
Method used for stress condition assessment – «sin2ψ» method and vertical exposure technique.
Radiation used – CrKα.
Check Points - between holes for flanges, along the perimeter of the holes, and at a 5 - 8 mm distance from the hole, and on the flanges being welded in.
Stress Condition Index – since it was required to assess, in each operation, the stress condition of the part on the whole, the stress condition index was selected as the mean stress value of all checkpoints. Stability of each technological operation was assessed by the standard deviation of reference sample.
Results Obtained If before flange welding the mean stress made–97 MPa, then after flanges were welded in, a change in the stress polarity into tensile stresses was observed: +665 MPa, and after thermal processing almost five-fold decrease in tensile stresses was noted: +138 MPa.
The most stable operation is thermal processing (the minimal reference sample deviation = 87 MPa), and the most unstable – welding in flanges (ÑÎ = 177 MPa).

|
Publications on the Subject X-ray diffractometer "RIKOR"
Determining Residual Stresses in Parts and Structures Made of Different Steels and Alloys, A.V.Kotelkin, A.D.Zvonkov, A.V.Lyutsau, D.B.Matveev, D.V.Dubrovin, V.N.Sereda, Abstracts Second International Conference on X-ray and Neutron Capillary Optics, Zvenigorod, Russia, September 22-26, 2004.
X-ray method of determining residual stresses in moldings and parts made of titanium, aluminum,
nickel; and other alloys / Kotelkin A.V., Zvonkov A.D., Lyuttsau A.V., Matveev D.B., Kumakhov M.A., Ibraimov N.S. – In Collected Articles: Die forging: perspectives and development (collected science reviews) – GOU VPO «UGTU-UPI», 2005. – pp. 784-790. (In Russian)
|
|
Application 2.
Stress Condition Check in Main Rotor Blades of Helicopter MI-8 Made of Aluminum Alloy
|

|
Object of check - seven main rotor blades of MI-8 helicopter made of alloy AVT-1. In this instance, vanes 0, 1, 2, 3, 4, 5, 6 had operation time of 370, 795,795, 1588, 1588, 1588 hrs, respectively.
Purpose of check – to determine correlation between stressed condition of the lower berth of blade longeron and operation time.
Check was done in the environment of one of Air Force divisions, with participation of A.V. Lyuttsau,
Dr. Eng. Sc. A.V. Kotelkin, Dr. Phys. Math. Sc. A.D. Zvonkov, Dr. Eng. Sc. D.B. Matveev, Dr. Eng.
Sc. V.N. Sereda, Dr. Eng. Sc. V. Ya. Maklashevsky.
|
Method used for stress condition assessment – vertical exposure method.
Radiation Used – CrÊα
Check Points – 21 points along the lower berth of blade longeron, equally spaced in between.
Stress Condition Index – since it was required to assess the condition of the part on he
whole in each operation, the stressed condition index was selected as the mean stress of all
checkpoints.
As the stressed condition index in each checkpoint, the first invariant of the principal stresses tensor was used: σ = (σ1+ σ2)/3. The confidence interval of the calculated stresses values under the exposure conditions used does not exceed 10 MPa (relative error is Δσav = +5 MPa).
|
Results Obtained
For all checked blades on the lower berth of longeron, strongly expressed heterogeneity of residual stresses lengthwise was observed, characterized by existence of areas where the residual stresses had undergone significant changes compared to original (vane 0). For each blade, the mean stress value along the length σav was determined (see the table). The resulting from correlation analysis Pearson coefficient equal to 0.73 evidences good correlation between σav and operation time.
Linear approximation of the dependence between the blade mean stress and operation time is shown on the figure. It follows from the obtained functional dependence that operation of the helicopter main rotor blades leads to a shift of the original level of compressing residual stresses towards tension.
|
Application 3.
Stress Condition Check in Aluminum Alloy Aircraft Wheel Hubs
|

|
Object of Check – two used aircraft wheel hubs made of alloy AK-6, one with strengthened working surface, the other one without.
Purpose of check – determining the difference between the stresses condition of aircraft wheel hubs with strengthened versus non-strengthened working surface.
Check was performed in the facilities of Moscow Institute for Steed & Alloys and Rubin AK OJSC, with participation of A.V. Lyutsau, Dr. Eng. Sc. A.V. Kotelkin, Dr. Phys. Math. Sc. A.D.Zvonkov, Dr. Eng. Sc. D.B. Matveev, Dr. Eng. Sc. Mozalev.
|
Method used to assess stress condition– «sin2ψ» method.
Radiation used – CrÊα. Check points – are depicted on the scheme.
Stressed Condition Index – in each checkpoint, two components of resid al stresses were
assessed: radial (σr) and tangential (σt).
Results Obtained
The results of determ on hub surfaces are given in tables 1 and 2.It follows from there that the strengthened hub had compressive residual stresses in all checkpoints whilethe non-strengthened – mostly tensile stresses shortening its life.
|
Table 1 Stresses on the Surface of Non-Strengthened Wheel |
Checkpoint
No.
|
st t, MPa
|
sz z, MPa
|
1-1
|
-90
|
+90
|
1-2
|
-180
|
0
|
1-3
|
0
|
+130
|
3-1
|
+20
|
-85
|
3-2
|
+120
|
-65
|
3-3
|
-205
|
-55
|
5-1
|
+150
|
+30
|
5-2
|
+170
|
+30
|
5-3
|
0
|
+25
|
9-1
|
+130
|
-
|
9-2
|
+65
|
-
|
9-3
|
+50
|
-
|
|
Table 2 Stresses on the Surface of Strengthened Wheel |
Checkpoint
No.
|
st, MPa
|
sz, MPa
|
1-1
|
-130
|
-330
|
1-2
|
-110
|
-200
|
1-3
|
-110
|
-370
|
3-1
|
-130
|
-190
|
3-2
|
-220
|
-310
|
3-3
|
-150
|
-370
|
5-1
|
-345
|
-370
|
5-2
|
-260
|
-320
|
5-3
|
-240
|
-370
|
9-1
|
-10
|
-
|
9-2
|
-70
|
-
|
9-3
|
-130
|
-
|
|
Publication on the Subject X-ray diffractometer "RIKOR"
X-ray method of determining residual stresses in moldings and parts made of titanium, aluminum, nickel; and other alloys / Kotelkin A.V., Zvonkov A.D., Lyuttsau A.V., Matveev D.B., Kumakhov M.A., Ibraimov N.S. – In Collected Articles: Die forging: perspectives and development (collected science reviews) – GOU VPO «UGTU-UPI», 2005. – pp. 784-790. (In Russian)
|
Application 4.
Stress Condition Check of Aluminum Alloy Tank of Refueler ATZ-20
|

|
Object of Check – tanks of refueller ATZ-20 of 20m3 capacity made of aluminum alloy 5086.
Purpose of Check was to determine stress condition of empty refueller tank, and when the tank was fiiled - mean effective stress
Check was performed at the primises of the Bykovo Aircraft Repair Workshop parking
s e, with participation of A.V. Lyuttsau, Dr . Eng. Sc. A. Kotelkin, Dr. Phys. Math. Sc. A.D. Zvonkov, Dr. Eng. Sc. V.S. Krasovsky.
|
Method used to determine stress condition – vertical exposure method.
Radiation used – CrÊα.
Checkpoints – in the most stressed tank part: around weld seam in the bottom.
Stressed Condition Index –since the requirements was to assess stress condition in each status of the tank on the whole, the stress condition index was selected as the mean stress of all check points.
|
Results Obtained
Before the tank was filled (status 1), mean stress made –110 MPa (mean standard sample deviation = 20 MPa), after it was filled (status 2): -55 MPa (mean standard sample deviation = 90 MPa). Consequently, the mean stress σe when the refueller tank is filled equals to +45 MPa (see the diagram).

Publication on the Subject X-ray diffractometer "RIKOR"
X-ray method of determining residual stresses in moldings and parts made of titanium, aluminum, nickel; and other alloys / Kotelkin A.V., Zvonkov A.D., Lyuttsau A.V., Matveev D.B., Kumakhov M.A., Ibraimov N.S. – In Collected Articles: Die forging: perspectives and development (collected science reviews) – GOU VPO «UGTU-UPI», 2005. – pp. 784-790. (In Russian)
|
Application 5.
Stress Condition Check of Chromium-Nickel Alloy Disks of Gas Turbine Engine
|

|
Object of check – six disks made of chromium-nickel alloy.
Purpose of check – was to determine influence of operation time on the stressed condition of strengthened disk surface.
Check was performed at the premises of Salyut MMPP, with participation of A.V. Lyuttsau, Dr. Eng. Sc. A.V. Kotelkin, Dr. Phys. Math. Sc. A.D. Zvonkov, Dr. Eng. Sc. D.B. Matveev.
|
Method used to determine stress condition – vertical exposure method.
Radiation used – CrÊα.
Checkpoints – on one of the sides of strengthened flat of each disk, 8 checkpoints in four sectors, which directions coincide with symmetry axes. In each of Â, C, D, and E directions, on desk part strengthened by surface plastic deformation four measurements were performed: checkpoint 1 – next to the hole, 2 –between the holes, 3 – under the hole, 4 – under the hole, closer to the collar (see the schematic)
Stressed Condition Index –since the requirements was to assess stress condition in each operation of the part of the whole, the stress condition index was selected as the mean stress of all check points.
Results Obtained
Residual stresses in disk checkpoints are very scattered both in terms of value and in terms of polarity: from –520 MPa to +200 MPa. This evidences large instability of the technological operation of disk flat strengthening.
|
The results obtained are given on the diagram. One can see that the first disk has the highest level of compressive stresses at the comparatively longest operation time while other disks at minimum operation time have the least level of compressive stresses. Consequently, depending on the quality of surface strengthening operation, the operation time affects differently on the change in the residual stresses level.
Publication on the Subject X-ray diffractometer "RIKOR"
X-ray method of determining residual stresses in moldings and parts made of titanium, aluminum, nickel;and other alloys / Kotelkin A.V., Zvonkov A.D., Lyuttsau A.V., Matveev D.B., Kumakhov M.A., Ibraimov N.S. – In Collected Articles: Die forging: perspectives and development (collected science reviews) - GOU VPO «UGTU-UPI», 2005. – pp. 784-790. (in Russian).
|
Application 6.
Stress Condition Check of Steel Landing Gear in Fighter SU-30MKI
|

|
Object of check – four main landing gears: 1 – landing gear without operation time; 2,3,4 – landing gears with operation time: 642; 1166; 1175 times used, respectively.
Purpose of check – was to determine correlation
between the stressed condition of landing gear and operation
time.
Check was performed in the premises of Sukhogo OKB OJSC, with participation of A.V. Lyuttsau, Dr. Eng. Sc. A.V. Kotelkin, Dr. Phys. Math Sc. A.D. Zvonkov, Dr. Eng. Sc. D.B. Matveev, Dr. Eng. Sc. A.A. Saanikov
|
Method used to determine stress condition – vertical exposure method.
Radiation used – FeÊα.
Checkpoints – 6 checkpoints close to weld seams.
Stress Condition Index – residual stresses of the unused landing hear were takes as zero, the stress condition index for other landing gears was the maximum, among six checkpoints, stress increment Δσmax (for subsequent calculation of remaining life).
|
Results Obtained
The results obtained are given in the table. Correlation analysis between the stress condition of landing
gear and its operation time shows good correlation between Δσmax and number of times the gear was
used (Pearson coefficient r equals to 0.73). Linear approximation of Δσmax dependence on operation
time is shown on the figure. It follows from the resultant functional dependence that landing gear
operation leads to a shift of the original level of residual stresses towards tension.
|
Table
Maximum Stress Increment for Each Gear and
Pearson Coefficient
|
Gear No.
|
Δσmax, MPa
|
Number of
Times Gear
Was Used
|
r
|
1
|
0
|
0
|
0,87
|
2
|
290
|
642
|
3
|
360
|
1166
|
4
|
720
|
1175
|
|

|
Application 7.
Stress Condition Check of Solid-Rolled Steel Railway Wheels
|

|
Object of check – solid-rolled wheel with standard cone-and-plate disk.
Purpose of Check – was to determine stress condition on the inner and outer sides of the wheel.
Check was performed at the premises of All-Russia Railways Transport Research Institute (VNIIZhT), with participation of Dr. Eng. Sc. A.V. Kotelkin, Dr. Phys. Math. Sc. A. D. Zvonkov, Dr. Eng. Sc. D.B. Matveev, A.V. Lyuttsau, S.L. Shitkin.
|
Method used to assess stress condition - «Sin2ψ» method.
Radiation used – FeÊα.
Checkpoints – 6 checkpoints on the rim; 10 checkpoints on the flat and 4 checkpoints on the center boss on each side of the wheel.
Stress Condition Index – was mean stress on the side in radial direction σRav.
|

Results ObtainedThe results obtained are given on the diagram. On the diagram, red color marks residual stresses on the inner side , green color on the outer side. On the inner side of the rim, rather large compressing
stresses only are effective; on the outer side, the residual stresses are practically absent. On the flat, compressive residual stresses are higher on the outer side. On the center boss, the residual stresses of compression on the inner side and of tension on the outer side are observed.
|
Diagram of Residual Stresses Level On Different
Wheel Sides

|
Application 8.
Stress Condition Check of the Locomotive Pinion Made of Steel 45ÕÍ
|


|
Object of check – a fragment of the locomotive pinion made of steel 45ÕÍ (Lyublino Foundry Mechanics Factory).
Purpose of check – was to assess the possibility of nondestructive quality control of pinions’ thermal processing based on residual stresses.
Check was performed in the premises of the Moscow Institute of Steel & Alloys, with
participation of Dr. Eng. Sc. A.V. Kotelkin, Dr. Phys. Math. Sc. A.D. Zvonkov, Dr. Eng.
Sc. D.B. Matveev, A.V. Lyuttsau, A.V. Shevchenko.
|
Method used to assess stress condition - «Sin2ψ» method.
Radiation used – FeÊα.
Check points on the butt end surface of pinion fragment, three checkpoints at the base of each
of six teeth.
Stress Condition Index – in each checkpoint, residual stresses were determined in tangential (X) and radial (Y) directions.
Results Obtained
The results obtained are summarized in the table.
|
Table
Residual stresses in checkpoints in radial and tangential directions
|
Tooth No.
|
Checkpoint No.
|
Check Results
|
σY, MPa
|
σX, Mpa
|
1
|
1-1
|
-83
|
-115
|
1-2
|
-1544
|
-119
|
1-3
|
-574
|
+90
|
5
|
5-1
|
-16
|
-574
|
5-2
|
-303
|
-349
|
5-3
|
-264
|
-350
|
2
|
2-1
|
-40
|
-131
|
2-2
|
-1081
|
-222
|
2-3
|
-728
|
+53
|
6
|
6-1
|
-1085
|
-207
|
6-2
|
-1149
|
-154
|
6-3
|
-1206
|
+59
|
3
|
3-1
|
-368
|
+26
|
3-2
|
-330
|
+30
|
3-3
|
-109
|
-110
|
7
|
7-1
|
-673
|
-470
|
7-2
|
-266
|
-57
|
7-3
|
-580
|
+118
|
4
|
4-1
|
-692
|
+906
|
4-2
|
-480
|
+263
|
4-3
|
-490
|
-546
|
|
One can see from the results obtained that all radial residual stresses σY feature the nature of compression. At that, significant variation is observed: from -1544 MPa to –16 MPa.
The situation with tangential residual stresses σX is much worse: together with effective stresses they
are responsible for crack formation at the teeth basis. There, along with compressive stresses, there are
zones with tensile residual stresses as well. The variation in the data obtained is even greater than for residual stresses: from –574 MPa to +906 MPa. The variation in value obtained (1480 MPa) is comparable to the elastic limit of steel 45ÕÍ. Such variation evidencess imperfectness of the existent operation of teeth surface thermal processing.
|
Application 9.
Stress Condition Check of Steel Weld Seam in Nuclear Power Industry
|

|
Object of check – weld joint made of structural steel.
Purpose of check – was to assess the possibility of nondestructive check of weld joints in nuclear power plant environment using portable x-ray diffractometer «Rikor».
Check was performed in the premises of a nuclear power plant, with participation of Dr. Phys. Math. Sc. A.D. Zvonkov, Dr. Eng. Sc. A.V. Kotelkin, Dr. Eng. Sc. M.B. Barikov.
|
Method used to assess stress condition - «Sin2ψ» method.
Radiation used – FeÊα.
Check Points – in the area of weld joint thermal impact.
Stress Condition Index – âin each checkpoint, residual stresses were determined in tangential (στ) and axial (σax) directions.
|
Results Obtained
The results obtained for residual stresses in axial (σax) and tangential (στ) directions in different
eld joint checkpoints are given on the figure. The work done showed the possibility of nondestructive
eck of weld joints in nuclear power plant environment using portable x-ay diffractometer «Rikor>>
|

|
|
Application 10.
Stress Condition Check of a Stainless Steel Measuring made tube fragment of steel 12Õ18Í10Ò
Fragment of Weld Joints in Nuclear Power Industry
|

|
Object of check – a fragment of weld joint made of austenitic steel.
Purpose of the check – was to assess stress condition of the weld int fragment in the seam and thermally affected area.
Check was performed in the premises of IRO LLC, with participation of A.V. Lyuttsau, Dr. Eng. Sc. D.B. Matveev, Dr. Phys. Math. Sc. N.S. Ibraimov, Dr. Eng. Sc. V.G.Lyuttsau, A.A. Bolotokov
|
Method used to assess stress condition - «Sin2ψ» method.
Radiation used – CrÊα.
Check points in the weld joint seamand thermally affected area.
Stress Condition Index– in each checkpoint, residual stresses were determined in axial direction.
|
Results Obtained
Residual stresses are presented on the figure below, where checkpoint 0 is the middle of the seam, checkpoints 1 and 6 are 9 mm, checkpoints 2 and 7 are 24 mm, checkpoint 3 and 8 are 45 mm, checkpoints 4 and 9 are 60 mm, checkpoints 5 and 10 are 24 mm, checkpoints 6 and 11 are 97 mm from the middle of the seam. At the bottom of the figure, the residual stresses in the weld seam and closer than 9 mm from it are presented. These stresses were obtained with the help of polycapillary collimation system of 0.5 mm in diameter.
|

|
Publications on the Subject X-ray diffractometer "RIKOR"
X-ray method of determining residual stresses in moldings and parts made of titanium, aluminum, nickel; and other alloys / Kotelkin A.V., Zvonkov A.D., Lyuttsau A.V., Matveev D.B., Kumakhov M.A.,
Ibraimov N.S. – In Collected articles: Die forging: perspectives and development (collected science
reviews) – GOU VPO «UGTU-UPI», 2005. – pp. 784-790. (in Russian).
|
Application11.
Stress Condition Check of Steel Gas-Line Weld Joint Fragment
|

|
Object of check – a fragment of gas pipe weld joint.
Purpose of check – was to assess stress condition of weld joint in thermally affected area of the gas line fragment having the operation time of τ2=17 years and that of gas line fragment with operation time τ1 = 0 years.
Check was done in the premises of All-Russia Gas Research Institute (VNIIGAZ), with participation of Dr. Eng. Sc. A.V. Kotelkin, Dr. Phys. Math. Sc. A.D. Zvonkov, Dr. Eng. Sc. D.B. Matveev, A. V. Lyuttsau, Dr. Eng. Sc. V.N. Sereda
|
Method used to determine stress condition – vertical exposure method.
Radiation used – FeÊα.
Check Points: three checkpoints at different distances from the longitudinal weld seam.
Stress condition index – (s1 + s2)/3.
Results Obtained
The diagramm represents residual stresses read from checkpoints 1…3 in case of 0 years operation time (red color), and 17 years operation time (green color). The data obtained show that the original level of tensile residual stresses in the said checkpoints considerably grows after seventeen years of operation, to a greater extend – in the nearest to the weld seam checkpoint, and to a lesser extend – in the third checkpoint.

|
Publications on the Subject X-ray diffractometer "RIKOR"
X-ray method of determining residual stresses in moldings and parts made of titanium, aluminum, nickel; and other alloys / Kotelkin A.V., Zvonkov A.D., Lyuttsau A.V., Matveev D.B., Kumakhov M.A., Ibraimov N.S. – In Collected Articles: Die forging: perspectives and development (collected science reviews) – GOU VPO «UGTU-UPI», 2005. – pp. 784-790. (in Russian).
|
Application 12.
Stress Condition Check of Steel Metal Columns of the Christ the Savior Cathedral
|
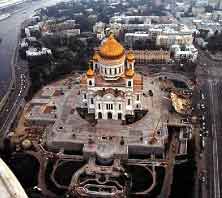
|
Object of check – four steel supporting columns in the ground floor of the Christ the Savor Cathedral (the Synod Cathedral).
Purpose of check – was to assess stress condition of the supporting metal columns.
Check was performed during construction in Moscow of the largest Christ the Savior Cathedral (Synod Cathedral), with participation of A.V. Lyuttsau, Dr. Eng. Sc. A.V. Kotelkin, Dr. Phys. Math. Sc. A.D. Zvonkov, Dr. Eng. Sc. D.V. Matveev
|
Method used to determine stress condition – vertical exposure method.
Radiation used – FeÊα.
Check Points – column base. Stress Condition Index – (s1 + s2)/3.
|
Results Obtained
Check has revealed that three columns were loaded equally. The fourth column was somewhat unloaded as regards other columns.

|
|
Application 13.
Stress Condition Check of Steel Elements of Bridges
|
Upon request from Gormost FGUP, the Krymsky and Borodinsky Bridges across the Moscow River were checked

|

|
Object of check – load- bearing chains and ties of the Krymsky Bridge, structural elements of the Borodinsky bridge
Purpose of check – was to assess stress condition of the structural elements of bridges.
Check was performed in Moscow condition with participation A.V. Lyutsau, Dr. Eng. Sc. A.V. Kotelkin, Dr. Phys. Math. Sc. A.D. Zvonkov, Dr. Eng. Sc. D.B. Matveev, Dr. Eng. Sc. N.I. Potapov
|
Method used to determine stress condition – vertical exposure method.
Radiation used – FeÊα.
Checkpoints – the most stresses points in the structural elements of bridges.
Stress Condition Index – (s1 + s2)/3.
Results Obtained
Stress check of the load- bearing chains, ties of the Krymsky Bridge in Moscow revealed the necessity of repair operations.
|
|
Application 14.
Physical Metallurgy Expertise of the Haulage Steel Rope of Lift No. 4 in the Ostankino TV Tower After Fire
|
The expertise waed at the Moscow State University of Steel and Alloys (Technological University) BPO GOY upon request of the RF General Public Prosecutor Office |

|
Object of check – two fragments of the haulage role of lift No. 4:
fragment ¹1 without evident traces of high temperature impact , and fragment ¹2 with noticeable traces of high-temperature impact. Purpose of check – to assess rope strength and nature of destruction
Check was performed in Moscow condition with participation A.V. Lyutsau, Dr. Eng. Sc. A.V. Kotelkin, Dr. Phys. Math. Sc. A.D. Zvonkov, Dr. Eng. Sc. D.B. Matveev, Dr. Phys. Math. Sc. J.N. Parhomenko
|
Results ObtainedPortable x-ray diffractometer of «Rikor» Series established change under the temperature impact in the condition of rope metal from hard-drawn (after manufacture) into thermally processed. This, together with other analyses, this enabled establishing the reason for rope destruction – it resulted from sort-time creepage under the action of high temperature and bears plastic nature.
|
Application 15.
Comparison of Residual Stress Values Obtained by XRD Method Using «RIKOR» Series Instrument Versus DAVIDENKOV Method
|

|
Object of check – disk fragment made of chromium – nickel alloy
Purpose of check - methods matching
Comparison was done in the premises of Moscow Institute of Steel and Alloys and Salyut NPO, with participation of A.V. Lyuttsau, Dr. Eng. Sc. A.V. Kotelkin, Dr. Phys. Math. Sc. A.D. Zvonkov, Dr. Eng. Sc. D.B. Matveev, Dr. Chem. Sc. N.S. Merkulova.
|
Out of a fragment of a disk made of chromium – nickel alloy, two samples were cut. The scheme of measurements to be done with «Rikor» Series Instruments for the samples prepared for the analysis to be done by the Davidenkov method is given in figure.
Thereafter samples were handed over to N.S. Merkulova, Salut NPO, for stress analysis following
the Davidenkov method using POVKON TENZOR plant. The resulting values of stresses along thickness
h of the samples obtained at the POVKON TENZOR plant Ð (Davidenkov method) are given on fig.2
(sample 1) and fig. 3 (sample 2). Straight lines D and E limit the interval of residual stress values obtained
using « Rikor » Series instrument. Curves  and Ñ show distribution of residual stresses in the surface in
case of consecutive removal with etching of the previous surface layer, which distribution was obtained
following the Davidenkov method.
DAVIDENKOV Method - Method of layer-by-layer chemical etching of one side of beam with a predeformed end. The Indentor mounted on the free end of the beam, based on the beam curvature, determines the residual stress value depending on the depth of the etched layer. It is widely used in aviation industry. It is a destructive method of checking (can be done only on samples).
|
Results Obtained
Almost one-hundred percent correspondence between two methods by mean residual stress values is
noted at a depth of four microns (according to Davidenkov:-225 MPa, according to XRD method:-229
MPA). Since for alloy EP741, the depth of half x-rays attenuation varies within 4-6 microns, the match of
the results obtained by the two methods, based on the mean value, can be assessed as ideal.
|
Application 16.
Stress Condition Check of Al2O3 Polycrystals (Polycor)
|

|
Object of check – 4 samples of rectangular Al2Î3 polycrystalline (polycor) plates.
Purpose of check - was to determine residual stresses in the samples.
Check was done in the premises of the Moscow Institute of Steel and Alloys withparticipation of A.B. Lyuttsau, Dr. Eng. Sc. A.V. Kotelkin, Dr. Phys. Math. Sc. A.D. Zvonkov, Dr. Eng. Sc. D.B. Matveev.
|
Method used to assess stress condition - «Sin2ψ» method.
Radiation used – CrÊα, indices HKL: {234}, peak in the area of Θ=680.
Check points - one check point in center of sample.
Stress Condition Index – in each checkpoint, the residual stresses were determined in two mutually perpendicular directions: σx and σy. Elastic constants used in the calculation were: the Young module - 380000 MPa, the Poisson coefficient - 0.3.
Results ObtainedThe results are given in the table.
|
Table |
Sample
No. |
σx, MPa
|
σy, MPa
|
1
|
-1130
|
-945
|
2
|
-1540
|
-1045
|
3
|
-610
|
-300
|
4
|
+80
|
-960
|
An example of sample diffractomgram
|

|
Application 17.
Stress Condition Check of Chisels Made of Steel 40Õ13 and Bronze OCS-555
|


|
Object of check - 1. A new puanson made of steel 40Õ132nme of about 300000 cycle.
2. A chisel having the operation time of about 300000 cycle within the temperature range of 20 ... 200 degrees C at 0 to 8 atmospheres pressure.
3. A chisel made of bronze OCS-555 with operation time of about 300000 cycles within the temperature range of 20…200 degrees C at 0 to 8 atmospheres pressure.
Purpose of check – was to determine residual stresses of chisels.
Chisels, Intercross LLC, were checked at the premisthe Moscow Institute of Steel and Alloys with participation es of of A.V. Lyuttsau, Dr. Eng. Sc. A.V. Kotelkin, Dr. Math. Sc. A.D. Zvonkov, Dr. Eng. Sc. D.B. Matveev
|
Method used to assess stress condition - «Sin2ψ» method.
Radiation used - FeKα, angle of diffraction Θ=55.7.
Checkpoints – in the area of chisel fins.
Stress Condition Index – since it was required to asses the stress condition of chisel in the vicinity of fins on the whole, the stress condition index was selected as the mean stress of all checkpoints.
Results Obtained
Mean stress on the fins of new chisel No.1 makes –240 MPa.
Mean stress on the fins of chisel No. 2 makes +72 MPa.
Mean stress on the finds of chisel No.3 withour cracks makes +190 MPa.
As a result of operation impact, residual stresses on the fins of the chisel made of steel 40Õ13 change their polarity (from compression –240 MPa to tension +72 MPa). For the chisel made of bronze the tensile stresses are even higher. Residual tensile stresses impose over effective tensile stresses leading, in the excess of the elasticity limit, to cracking.

|
Publications on the Subject X-ray diffractometer "RIKOR"X-ray method of determining residual stresses in moldings and parts made of titanium, aluminum, nickel; and other alloys / Kotelkin A.V., Zvonkov A.D., Lyuttsau A.V., Matveev D.B., Kumakhov M.A., Ibraimov N.S. – In Collected Articles: Die forging: perspectives and development (collected science reviews ) – GOU VPO «UGTU-UPI», 2005. – pp. 784-790. (in Russian).
|
Application 18.
Stress Condition Check of a Cast Iron Forming Roll Fragment
|

|
Object of check - a forming roll fragment made of gray cast iron with a surface layer of white cast iron.
Purpose of check - was to determine residual stresses of the fragment.
Check was done at the premises of IRO LLC with participation of A.V. Lyuttsau, Dr. Eng. A.V. Kotelkin, Dr. Phys. Math. Sc. A.D. Zvonkov, Dr. Eng. Sc. D.B. Matveev, Dr. Phys. Math. Sc. N.S. Ibraimov, A.A. Bolotokov
|
Method used to assess stress condition - «Sin2ψ» method.
Radiation used – CrÊα,
Checkpoints - the first checkpoint is on the working surface of the iron forming, the second - in the surface layer of white cast iron close to the working surface, the third one – in the gray cast iron layer far from the working surface.
Stress Condition Index - in each zone, residual stresses in tangential direction wedetermined.
Results Obtained
On the working surface of the forming roll (checkpoin 1) the obtained level of residual stresses is close to nil. In the tangential direction , in the surface layer of white cast iron (checkpoint 2), tensile stress was observed (+90 MPa); further, in the gray cast iron layer (checkpoint 3) there were compressive stresses (- 60MPa).

|
Publications on the Subject X-ray diffractometer "RIKOR"
X-ray method of determining residual stresses in moldings and parts made of titanium, aluminum, nickel;and other alloys / Kotelkin A.V., Zvonkov A.D., Lyuttsau A.V., Matveev D.B., Kumakhov M.A., Ibraimov N.S. – In Collected Articles: Die forging: perspectives and development (collected science reviews) – GOU VPO «UGTU-UPI», 2005. – pp. 784-790. (in Russian).
|
Application 19.
Stress Condition Check in Steel ShKh15 Steel Round Billets
|

|
Object of check – four billets for fabrication of ball- bearing rings made of steel ShKh15, two had scale on the surface, the other two were free of surface.
Purpose of Check – was to determine residual stresses of billets.
Check was done at the premises of the Moscow Institute for Steel and Alloys with participation of A.V. Lyuttsau, Dr. Eng. Sc. A.V. Kotelkin, Dr. Phys. Math. Sc. A.D. Zvonkov, Dr. Eng. Sc. D.B. Matveev, D.B. Dubrovin
|
Method used to assess stress condition - «Sin2ψ» method.
Radiation used - FeKα
Checkpoints – in the area of stress. Stress Condition Index – in each zone, residual stresses were determined in axial (z) and tangential (τ) directions.
Results Obtained
The inspection results are given in respective bar carts (samples 1, 2, 3 and 4 are marked with red, green, blue, and light blue color, respectively).

Stresses in axial direction do not ultimately render much influence on ovality of billet since those are partially eased in the course of tube cutting into rings. Much greater influence on ovality is rendered by residual stresses. The data obtained show that in tangential directions billets 1, 3 and 4 reveal residual stresses of different polarity, which may lead to their ovality during their further processing.
|

|
Publications on the Subject X-ray diffractometer "RIKOR"
X-ray method of determining residuade of titanium, aluminum, nickel; and other alloys / Kotelkin A.V., Zvonkov A.D., Lyuttsau A.V., Matveev D.B., Kumakhov M.A., Ibraimov N.S. – In Collected Articles: Die forging: perspectives and development (collected science reviews) – GOU VPO «UGTU-UPI», 2005. – pp. 784-790. (In Russian).
|
|
Call us over the contact phones or e-mail for additional information !!!
|